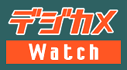 |
 |
 |
 |
最新ニュース |
 |
 |
【 2016/01/26 】 【 2016/01/25 】 【 2016/01/22 】 【 2016/01/21 】 【 2016/01/20 】
|
|
 |
 |
 |
 |
 |
オリンパス中国工場レポート(後編)
|
 |
~E-510を組み立て、梱包して、出荷するパンユウ工場
|
 |
 |
 |
 |
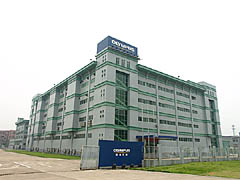
|
E-510の組み立てを担当するパンユウ工場
|
~前編はこちら
前編に続きE-510製造現場のレポートをお届けする。
現在の番禺工場は、シンセン経済特区から車で1時間ほど西へ向かった広州市番禺区に2002年10月に建てられた。
番禺(以下、パンユウ)区は、シンセン市のような経済特区は持たないが、港が近いこともあってパンユウだけでなく、周辺都市にも日系企業や委託でカメラ用の部品などを製造する協力会社も多い。
前身となる工場を立ち上げたころはシンセン・パンユウ間を流れる珠江には橋がかかっていなかったので、物資の輸送や出張する日本人スタッフも渡し船を利用していた。しかし、今では巨大な吊橋と近代的な高速道路が開通し、2つの街の往来は年々楽になってきているという。
同工場のデジタルカメラ関係の主な業務は、シンセン工場などで製造された部品による実装と組み立てとなっている。そして、完成した製品はこの工場で梱包して世界中の現地法人へと出荷される。
業務を具体的に説明すると、ペンタダハミラー式のファンインダー、撮像素子、ローパスフィルター、液晶モニターなどあらゆる部品を集めて、デジタル一眼レフカメラE-510やE-410や、深度10mまで撮影できるコンパクトデジタルカメラμ770SWなどを組み立てている。
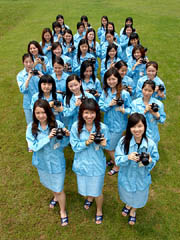
|
E-510とE410の組み立てを担当する女性従業員たち
|
2007年のデータでは、パンユウ工場の敷地面積は3万3,415平方m、従業員数が4,770人、主な生産品目は「デジタルカメラ」と「録音機」、デジタルカメラの年間生産能力はデジタル一眼レフカメラが100万台、コンパクトデジタルカメラが500万台。工員のほとんどは省外からやっていきた20代の女性たちであり、男性は180人しかいない。
コンパクトデジタルカメラの業務は2003年1月にμ 10 DIGITALから始まり、デジタル一眼レフカメラ関係の業務は2004年11月のE-300から始まっている。
■ パンユウ工場の製造現場を訪問
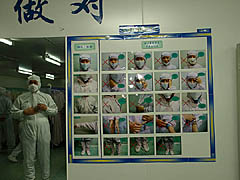
|
クリーンルームに入る前に鏡の前で身なりを整える。防塵服の着用に間違いがないかチェックする
|
デジタル一眼レフカメラの製造場所は主に2つに分けることができる。それらは一般作業室と、清浄度が厳しく管理されたクリーンルームだ。シンセン工場などから届けられた部品は、まず一般作業室で仕分けされてゴミが出る可能性のある作業はすべてそちら側で行なわれる。その後、十分に埃などを落とした後でクリーンルームへと搬入される。
また、クリーンルーム内で働く従業員は頭からつま先までつながった防塵服を着用する必要がある。もちろん、マスクの着用も不可欠だ。オリンパスの埃に対するこだわりは大変に厳しい。それは同社がEシステム誕生当初から撮像素子への光の到達を阻むゴミを防ぐ「ダストリダクションシステム」を採用していることも関係している。つまり、埃の影響を受けることなく撮影できるはずのカメラに、製造時に埃が入っているようではあまりにも恥ずかしい。ユーザーとしてはとても歓迎できる製造ポリシーだ。
今回は、発売間近のE-510の製造ラインを見学することができた。すでに量産機の製造は始まっており、発売開始に向けて可能な限りのストックを作っている真っ最中だった。
|
|
防塵服の構成は、頭巾、マスク、そして靴まで一体となったスーツの3点セット
|
防塵服を着た後は強風を全身にあてて埃を吹き飛ばしてからクリーンルームへ入る
|
オリンパスでは2004年より、イスを使用しない立ち姿による流れ作業を取り入れている。1ユニット=1ラインというチーム単位で作業が行なわれる。
製造ラインは細かい部品を作る縦方向のラインが無数に存在する。そして細かい部品は1本しかない縦方向のラインへと集約されて、カメラボディなどの製品が完成する。
ライン内ではベルトコンベアーを使わずに、従業員から次の従業員へと手渡してパーツを流していく。これは製作スペースの節約に役立つだけでなく、従業員同士のコミュニケーションとしても有効な手段だという。
最初に見学したのは、E-510の最大の特徴である手ブレ補正機能「iS」のユニットの製造作業。熟練の作業者がハンダやシールを使って細かい部品を組み立てて1つ1つのユニット(部品の集合体)に仕上げていた。
|
|
手ブレ補正ユニットの部品を取り付ける
|
基板裏側が傷つかないように専用の台の上で作業を行なう
|
|
|
基板同士の接点をピンセットを使って1つ1つ慎重につなぐ作業
|
手ブレ補正部、ダストリダクション部、受光部などの3つのメカが集まって1つのユニットとなる
|
ミラーユニットを組み立てる作業。指サックをはめた指で細かい部品が次々と組み上げられて、やがて1つのユニットになる。できあがったユニットはボディ組立ラインへと流されて、そのまま組み上げられる。
|
|
ミラー部本体をサックをした指で扱っている
|
ミラーをスイングできるようにユニットはめているところ
|
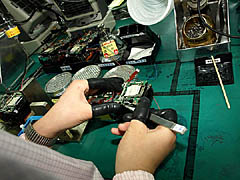
|
メモリカードスロット部をボディに取り付けている
|
メモリカードスロットをボディに取り付けて電気接点同士をつないでいる。同社の製品はCFとxDピクチャーカードのダブルスロットを採用しているので、ユニットとしてはやや大きい。
大きなユニットを小さなボディに取り付ける苦労には頭が下がる。ダブルスロット方式は今後も継続して欲しい。
ファインダーの取り付け作業。ペンタダハミラーや射出成型で製造された接眼レンズなどを組み上げたファインダーユニットとボディに取り付ける。とても小さなネジを電動ドライバで回して取り付ける作業者の表情は真剣そのもの。
|
|
E-510のボディ上部。ここにファインダーユニットを取り付ける
|
作業状況がわかりやすいように退いて撮ってみた
|
|
|
E-510のボディにファインダーが組み込まれたところ
|
ファインダーの接眼部周辺を組み立てているところ
|
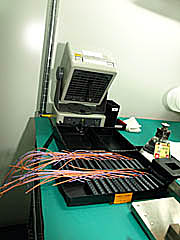
|
内蔵ストロボのコンデンサー。組み込む瞬間まで静電気防止のためにイオナイザーでイオンを含んだ風をあてている
|
内蔵ストロボ用のコンデンサーを取り付ける作業。大容量の電気を取り扱う部品だけに、取扱いには最細の注意が必要だ。なお、コンデンサーの上にある機械はイオナイザー。イオンを含んだ風を備品にあてて静電気の発生を抑えている。
組立作業が進んでやっとカメラらしい外見になってきた。中身が出来たら、まずは前面の外装をはめて、外装の操作系スイッチと組み上げたボディとの電気的な接続を行なう。最後にファインダーマットが取り付けられ、工程保証を行なうためのテスターが厳しい検査を実施する。検査を通った製品だけが次のラインへと流される。
|
|
内側が組みあがったE-510。デリケートな部分がまだむき出し
|
外装を取り付けているところ。操作系をボディ内側と1つづつ接続する
|
|
|
ボディ外装の前後をはめているところ
|
メモリスロットカバーを取り付けているところ
|
組み上がった製品は、すべて所定の作動チェックが行なわれる。流れ作業なので隣の作業員から渡される個体を、1人1人が担当する箇所をチェックする。
内蔵ストロボのポップアップや発光、各部ボタンやダイヤルなどすべての操作ボタンを検査する。おかげで製造ラインの中でここだけは操作音や作動音がやかましかったり、何の前触れもなしに閃光を繰り返したりと落ち着かない雰囲気だ。最後に、AFなどのチェックのために試写も行なわれる。
|
ファインダーをのぞきながらAFの作動を確認する
|
製品チェックが終わったE-510は、マニュアルや付属品などと一緒に化粧箱へ梱包される。ちょうどこのときは、北米市場向けのイーボルト(E VOLT)E-510の梱包が行なわれていた。イーボルトは北米市場でのEシリーズの愛称。ただし、E-510の場合、化粧箱にはイーボルトの文字はあるが、製品ボディにはプリントされていないので、箱に詰められる製品は日本市場向けとまったく同じものだ。
|
|
充電器やマニュアルなどと一緒にE-510を化粧箱に詰め込む
|
ビニールで包む前にE-510の最後の拭き清掃が行なわれる
|
化粧箱に詰められたE-510は、今度は出荷用(輸出用)の梱包が施される。この後は空港に運ばれて、同製品を首を長くして待つ世界中の現地法人へと送られる。これでオリンパスの中国工場で行なわれるE-510の製造工程が完了する。
|
|
E-510は梱包後にパンユウ工場から出荷される。行先はもちろん海港ではなく空港だ
|
輸出先の現地法人の倉庫にはこの姿で到着する。つまり工場では国際貨物対応梱包のテクニシャンも働いているのだ
|
■ パンユウ工場インタビュー
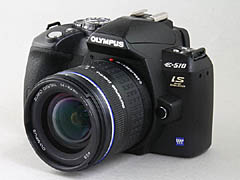
|
パンユウ工場で組み立て作業が行なわれているデジタル一眼レフカメラ「E-510」。7月発売でオープンプライス。店頭販売価格は11万円前後の見込み
|
中国の工場を実際に訪れる前に、案内役のオリンパスの方々との世間話の中に、1つ予想外の話があった。E-510とE-410は、ボディの小型化がいっそう進んだために、製造現場ではかなり無理をしているのかと思っていたのだが、「設計的な無理はしていないので、新型であっても手ブレ補正ユニット以外はすべて従来機で培った経験があれば組立は容易である」というのだ。
そこで、筆者の素朴な疑問をパンユウ工場で従業員達を指導する立場にある中国人リーダー5人に聞いてみた。製品の試作段階から日本の開発サイドと検討を繰り返し、実際に中国で効率的な製造方法を考え出し、現場の従業員を指導するという最前線にいる彼らの、同機に対する共通した印象は4つあった。
- 機能性が高くカメラとしての設計に優れている
- 可能な限り組み立てやすくなるような設計が施されている
- 十分に組立技能をもった従業員が製造にあたっている(以前はE-500の製造を担当していたチーム)
- 製造ラインも非常に効率のよいものを組むことが出来た。
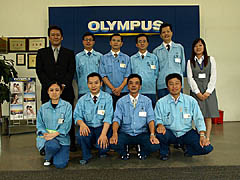
|
インタビューに応じてくれたパンユウ工場の日本スタッフと中国人リーダー(プラス通訳さんと工場受付嬢)
|
E-510には手ブレ補正ユニットという同社初めての機能も搭載されていて、これには最初は手こずったということだ。しかし、製造する側から見ても無理のない設計なので、工程の7割程度は作りやすいという印象を持っているとのことだ。
まとめとして、5人のリーダーたちの生の声を日本のオリンパスユーザーへ届けたい。愛社精神に満ちたコメントではあるが、その中に彼らの製造に対する強固な自信と高い義務感が感じられる。
技術リーダーの劉(リュウ)氏は、「製造を始めたころの話ですが、組み立てる部品の質を安定させるまでは少々苦労しました。しかし、E-300から続くデジタル一眼レフカメラの製造時に起こった問題の克服を通して、ミスや問題の発生への対処する経験が相当に蓄積されました。E-510に特化した新たな製造ラインを採用した理由もありますが、新型であるE-510であっても製造業務は思ったよりも困難ではありません。我々にとって製造する上で一番プレッシャーが掛かるのは防水機能をもつコンパクトデジタルカメラμ770SWです。これと比べればデジタル一眼レフの製造は比較的容易なので、まったく新しい製品であっても高い品質の実現は可能です」
組立グループリーダーの張(チョウ)氏は、「はじめてE-510を目にしたときはとてもキレイなカメラと思った。実際に作ってみて、弊社が初めて搭載した手ブレ補正機能は同様の機能を持つ他社製品にも引けを取らないことがわかった」と語ってくれた。
製造部リーダーの何(ホウ)氏は、「我做我能!(私は実行する。私はできるの意味)のスローガンの通り、E-510を世界最高の品質で市場へ送り届けるという我々の義務を実行します」と語ってくれた。
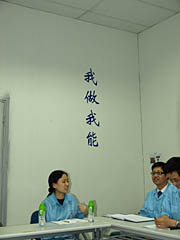
|
「我做我能」は従業員が考え出した2006年度のスローガン
|
品質管理者の李(リー)氏は「E-510を製造できることを誇りに思います。工場のすべての従業員が完美品質(品質100%)の製品をユーザーの手元へ届けるために努力しています」と語ってくれた。
パンユウ工場E-510工場リーダーの周(シュウ)氏は「E-510の品質は世界で一番高いと自信を持っています。欠点はゼロです!」 。
|
|
写真食堂の風景。平均年齢は21歳。シンセン工場と同じくほとんどが女性。この日のメニューはニンニクの芽と豚肉の炒め物などだった
|
社員食堂の風景。ご飯とオカズのセットで食事代は1食1.5~2元。5元のスペシャルランチもある。支払は非接触式のICカードで行なわれる
|
中国語のスローガンの表記に間違いがありました。「我故我能」ではなく、正しくは「我做我能」です。お詫びして訂正いたします。
■ URL
オリンパス
http://www.olympus.co.jp/
オリンパス E-510 関連記事リンク集
http://dc.watch.impress.co.jp/cda/dslr/2007/03/12/5812.html
■ 関連記事
・ オリンパス中国工場レポート(前編)(2007/06/06)
( 本誌:織原 博貴 )
2007/06/07 02:15
・記事の情報は執筆時または掲載時のものであり、現状では異なる可能性があります。
・記事の内容につき、個別にご回答することはいたしかねます。
・記事、写真、図表などの著作権は著作者に帰属します。無断転用・転載は著作権法違反となります。必要な場合はこのページ自身にリンクをお張りください。業務関係でご利用の場合は別途お問い合わせください。
|
|
|
|

|
 |