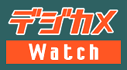 |
 |
 |
 |
最新ニュース |
 |
 |
【 2016/01/26 】 【 2016/01/25 】 【 2016/01/22 】 【 2016/01/21 】 【 2016/01/20 】
|
|
 |
 |
 |
 |
 |
シグマのレンズ工場見学記
|
 |
~タイムリーな新製品投入の秘密は内製化に
|
 |
 |
 |
 |
一眼レフデジタルカメラの低価格化、普及により、今後の市場拡大が見込まれる交換レンズ市場。しかし、かつての銀塩一眼レフ全盛期とは決定的に異なる部分がある。それは交換レンズに求める質のレベルだ。
銀塩時代、一般ユーザーの撮る写真はサービス判プリントが中心で、一部の写真だけを引き伸ばして見る程度。無論、強い純正指向があったことも影響しているだろうが、交換レンズメーカーに求められていたのは、何よりも価格の安さだった。
ところが誰でもカンタンにピクセル等倍で写真を見ることができるデジタルの時代。その是非はともかくとして、レンズに求める性能レベルは以前よりも格段に上がっているという。ズームの高性能化が進んだ現在にあって、単焦点レンズにも人気が集まる現象を見る限り、レンズに対するユーザーの画質指向の強さには驚かされる面もある。
そうした市場環境の変化の中、デジタル一眼レフユーザーにいち早くコミットし、存在感を増しているのがシグマだろう。同社取締役副社長の山木和人氏自身、品質指向の物作りが可能になってきた現状を喜ぶコメントをインタビューの中でしていた。
加えて同社の矢継ぎ早とも言えるデジタル専用レンズの開発。銀塩市場とデジタル市場が混在する現在、デジタル専用レンズのモデル数増加は経営面での大きなリスクも伴う。果たしてここまでの素早い製品開発の裏にはどのような背景があるのか。
福島県会津磐梯にあるシグマのレンズ工場を訪ねてみた。
■ あらゆる要素を垂直統合
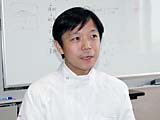
|
シグマ 取締役副社長の山木和人氏
|
シグマ製交換レンズはすべて、取材した会津の工場で生産されている。その規模は敷地面積8万平方m、建坪3万3,000平方mという広大さで、従業員1,000人が交換レンズの生産に関わっている。交換レンズの生産キャパシティは日産4,000~4,500本、月8万本で、ほぼフル稼働で生産する交換レンズ専門工場である。
山木氏は「シグマの場合、レンズ製造に関わるあらゆる要素をすべて社内で垂直統合し、会津工場に集約しています。このため交換レンズ工場としては世界でも屈指の大規模工場になっているのです」と説明する。
その言葉通り、工場内は多数の町工場の集合体のようだ。
工場内の様子はレンズ生産工程とともに後述するが、レンズ製造に関わるあらゆる要素が会津工場にはある。レンズそのものの研磨やコーティング、非球面加工はもちろん、金属部品の加工、塗装、文字入れに至るまで自社で行なう。それどころかプラスティック部品の金型製作、射出成形、塗装なども自社内でこなす。
その一方で、専用シャフトの削りだしや絞り羽根のパンチ加工など、実に細かな部品を作っている場所まであり、別の場所へと足を踏み入れると電子部品の実装が行なわれているといった具合だ。
レンズの場合、もちろん人の手による細かな調整など組み立て工程における品質と生産性の向上も競争力を高める上で重要だろうが、シグマ会津工場の最大の武器は何か?と言えば、それは徹底した垂直統合による内製化比率の高さにあるのかもしれない。
とはいえ、ここまであらゆる要素を統合すると、製造に利用する加工機械や検査装置の償却やメンテナンスなど、経営者側の負担は非常に大きなものになる。たとえば金型製作のためのマシニングセンターだけでも、ざっと見ただけで8台程度が稼働していた。まるで機械加工専門工場のように見える。
「実際、自社であらゆる要素を垂直統合するのは大変で、リスクをいかに避けていくか経営側の負担は大きい。しかし可能な限りの高品位と低価格をバランスさせるためには、内製化比率を高める事がもっとも有効です。細かな部品加工を外注していたなら、我々はここまで製品の低価格化を行えなかったでしょう(山木氏)」。
■ 内製化がタイムリーな製品投入を支える
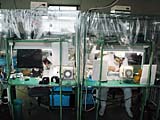
|
工場内には製品の修理を行なうサービス部門もある
|
加えて内製化比率の高さは、製品のタイムリーな投入にもつながる。新設計のレンズを量産ラインに載せる際、立ち上げ初期には細かな仕様変更が繰り返し行なわれるものだ。社内ですべての部品を作れる体制を築いているからこそ、開発サイクルを早めることが可能になる。デジタル専用のDCレンズを発表以降、ニーズの高い焦点域の新製品を多数投入できているのは、製造現場からのフィードバックを素早く前工程に反映できる体制があるからこそだ。
「最新の技術を素早く取り入れるという意味もあります。また、新しい技術に挑戦した時、外部に依存していたのでは社内に設計・製造のノウハウが残りません。細かな部分にまで拘って製品を改善するには、自分たちで手を汚して、汗をかいて、それを次の製品に活かしていかなければならない。そうでなければ前へは進めないというのがシグマのポリシーです」と山木氏は胸を張る。
たとえばシグマでは、複合非球面とグラスモールド非球面の両方を自社で生産する技術を持っている。もっとも、一言で非球面といっても、そのレベルは様々。一足飛びではなくとも、少しづつノウハウの蓄積で非球面レンズの複雑度や品質も上がる。自社で加工しなければ、当然ノウハウも蓄積できないわけだ。
低コストに少しづつ前へと進み、品質を上げて行くには、すべてを自社生産で行なうのがもっとも良い。それを創業以来、継続してきたねばり強さが現在のシグマの競争力を生んでいるのかもしれない。
ちなみに会津工場では一眼レフカメラの製造も行なわれている。Foveonセンサーを用いたSDシリーズは、会津工場の一角にあるクリーンルームで作られており、エンジニアリングプラスティックのボディなども、金型から成形、塗装まで工場内で一貫生産される。
■ ユーザーの目がシグマレンズの開発を変える
さてデジタルへの市場変化が、より高い品質の交換レンズを求める流れを生み出していると述べた。すなわちユーザー自身の目が、レンズ開発そのものの方向を変えたというわけだ。
「ピクセル等倍で見る事に対する賛否両論はありますが、そこでピクセル等倍で見るものではない、と言っても仕方ありません。ユーザー自身がより収差の少ないレンズを求めているのですから。一眼レフカメラは交換レンズとのシステムで撮影を行ないます。レンズが変われば写真も変化する。レンズのバリエーションが拡がれば、撮影の幅も拡がります。またフィルムとCCDという違いも、レンズに対して変化を求めています(山木氏)」。
山木氏によると、デジタル時代になってもっとも大きく変化したのはレンズコーティングだという。かけられるコストが同じなら、どこにコストをかけるべきか。注力する部分がコーティングへと変化している。
レンズコーティングはドーム型のフレームにレンズを1枚づつ人手でセットし、それを釜の中に入れてコーティング材料を蒸着させる。会津工場ではコーティングもすべて工場内で行なっているが、以前よりもコーティングにかける工程は増えているという。これにはコーティングを行なう機械の進歩もある。
「たとえば低分散ガラスは通常の光学ガラスよりも柔らかく、熱の変化で割れやすいため、コーティング後、急激に冷やすことができず、釜の中で自然冷却しなければなりませんでした。これが製造コストを押し上げる原因にもなっていたのですが、現在は冷却用の釜を併設し、コーティング後に冷却釜に移し、スグに次のレンズにコーティングを施せるようになりました。こうした細かな製造装置の進歩があって、低価格でも高品位のコーティングが行えるようになっています。同じような変化は様々な部分で起きていますが、そうした技術革新をいち早く取り入れられるのも、シグマの垂直統合型工場だからです」と山木氏。
もっとも品質を求めるユーザーの目は、意外なところで無用なコストアップも生み出しているのかもしれない。
「交換レンズは単体で見た時の美しさも評価されます。レンズを外し、透かして見て、ゴミやキズを探すことができてしまう。本来なら被写界深度から外れていたり、センサー部分とは関係のない部分で性能的には問題がないレベルでも、交換レンズの場合はNGとなってしまいます。そうした性能とは関係のないゴミや見た目の美しさを出すため、実は相当に大きなコストをかけて開発・製造を行なっています(山木氏)」。
言い換えれば、そうしたオーバークオリティな部分を求められなければ、本来の写りに関係するところにコストをかけられるわけだ。ユーザー側から見ればショッキングな面もあるが、交換レンズの商品性を考えればやむを得ない部分もある。
山木氏は「交換レンズとはそういう性質の製品です。オーバークオリティというのではなく、ユーザーの目が求める品質レベルと考えて、良品率を上げる努力をしています」と話した。限られたコスト内で高品位なレンズを求めシグマの挑戦は続く。
【交換レンズの製造工程】
交換レンズの製造工程は大きくレンズ加工、金属部品加工、エンジニアリングプラスティック部品加工、プレス部品加工、電子部品加工に分かれ、最後に各パーツを集めて組み立てが行なわれる。それぞれの工程を写真で追いかけてみよう。
■ レンズ加工
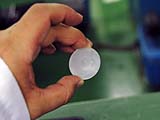
|
メーカーから届いた硝材はおおまかにレンズ形状に近づけてある
|
レンズの元になるガラス部品、硝材はガラスメーカーから購入している。硝材は光学ガラスをダイレクトにプレス加工し、目的のレンズ形状に近似させたものだ。
これを粗摺(あらずり)工程で研磨し、レンズ形状に近づけ、精研(せいけん)工程でレンズとしての精度を出す。これをさらに細かく滑らかな表面に研磨して最終精度を出し、コーティング、芯取り、墨塗・接合を経てレンズができあがる。
|
|
|
粗摺は自動化されている
|
中央の円盤状の砥石がレンズを研磨する
|
粗摺後の硝材。まだ透明になっていない
|
|
|
|
精研工程も自動化されている
|
精研中
|
精研後のチェック
|
コーティングはレンズをドーム状のフレームにはめ込み、カマの中に入れて薬品を蒸着させる。ドームの内側から薬品が付着するため、片面の処理が終わると、今度は逆側のコーティングも同じようにやらなければならない。
|
|
|
コーティング用のフレームにレンズをはめる
|
コーティング用のカマ。部屋の外からしか見ることができなかった
|
コーティング用のフレームからレンズを取り出しているところ。レンズのチェックをしながらのため、暗い部屋で作業する
|
芯取りとはレンズの中心を正確に出す工程で、検査装置でレンズセンターを読み取り、センター部分を中心に回転させ、小端(コバ)を削り落とすことでセンターズレのない真円のレンズとする。
非球面レンズの場合、研磨後に非球面加工用の特殊なプレス加工装置を用い、技術者がひとつひとつのレンズに非球面形状を作っていくそうだが、この工程は“マル秘”との事で、遠目にしか見ることはできなかった。
|
|
芯取り工程
|
検査機器のモニターを見ながら、レンズを真円にしていく
|
墨入れはレンズの周り(側面)を内面反射防止のために黒く塗る工程だが、これがなかなか面白い。キレイに塗るためには人の手が不可欠で、機械化がもっとも難しい工程のひとつだとか。反射防止塗料を平筆につけ、工員がひとつひとつ、回転するレンズ側面に軽く筆を押し当てて墨入れを行なう。なお、接合工程は色収差を取るための接合レンズを作るときのみ必要な接着行程だ。
|
|
墨入れは工員がひとつひとつ行なう
|
回転するレンズ側面に筆を押し当てて墨を塗る
|
■ 金属部品加工
材料はパイプ材とダイキャストを購入し、RC旋盤などで加工し目的の部品を作る。鏡筒などはもちろん、細かなシャフトなども自社で加工していた。
加工後の材料はアルマイト処理を施すが、アルマイト処理ももちろん自社内で行なっている。加工前に部品をセットするための治具まで自作する徹底ぶりだ。最後に塗装や文字入れを行なって仕上げる。
■ エンジニアリングプラスティック部品加工
材料はペレットで購入するが、その後のすべての工程は会津工場内にある。自社製品のすべての金型は工場内で設計され、マシニングセンターで削りだして作っており、保管場所には無数の金型が並ぶ。後述するプレス部品用の金型もここで作る。
射出成形装置に金型を設置し、装置を動かすとプラ部品が次々にできあがる。プラ部品の塗装部門も工場内にある。シグマ製レンズの付属フードには、きちんとつや消し塗装が施されたものが多いが、それも社内で塗装を行っているからこそできるのだろう。
|
|
|
プラスチックの材料のペレット
|
成型されたプラスチック部品
|
塗装されたプラスチック部品
|
|
|
|
金型
|
工場内には大量の金型が保管されている
|
金型の製造も自社で行なう
|
■ プレス部品加工
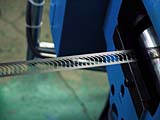
|
絞り羽根を打ち抜いた後のプレート
|
打ち抜き用の金属プレート/リボンなどの材料は購入だが、前述したように金型は自社製だ。
■ 電子部品
工場内にハンダ槽やチップ部品のマウンターがあり、電子部品の製造も自社で行なっている。
|
|
|
基板にチップをのせるマウンター
|
マウンターから出てきた基板
|
手作業でのハンダ付けも行なわれている
|
■ 組み立て工程
組み立て工程は見慣れた組み立て工場の様子に近いが、所々を注視するとフォーカス精度の微調整など重要な工程がその中に入っている。フォーカス精度は測定装置を見ながらフォーカスレンズの移動部にワッシャーを挟むなどして合わせ込む。
|
|
|
組み立て工程
|
フォーカス機構の微調整
|
調整用のワッシャーが見える
|
(撮影:田中真一郎)
( 本田 雅一 )
2005/05/30 00:01
・記事の情報は執筆時または掲載時のものであり、現状では異なる可能性があります。
・記事の内容につき、個別にご回答することはいたしかねます。
・記事、写真、図表などの著作権は著作者に帰属します。無断転用・転載は著作権法違反となります。必要な場合はこのページ自身にリンクをお張りください。業務関係でご利用の場合は別途お問い合わせください。
|
|
|
|

|
 |